special parts
We offer suitable solutions for your (special) requirements!
Over the last few decades, a variety of manufacturing options have developed. Technological progress in the manufacturing industry offers a wide variety of solutions for the implementation of manufactured articles according to drawings. We too had to keep up with the times and adapted our portfolio to meet the requirements and needs of our customers.
Based on your production drawing or the production drawing created by us, we can offer you exceptionally good market conditions through the targeted selection of suitable manufacturing processes.
In addition to domestic direct production on an EU basis, through nearby European countries to our Asian plants — we can check which production location provides the greatest benefits, depending on the needs situation and customer requirements.
Determining the optimal manufacturing technology
The right selection of the right manufacturing technology opens up great opportunities; expensive manufacturing processes can now be replaced by new, more economical production methods. The analysis of the most economical manufacturing processes plays a decisive role here and forms the basis for the further calculation of new articles. In doing so, we rely on both our internal manufacturing know-how and the expertise of our manufacturer network — which enables us to achieve a comprehensive article review.
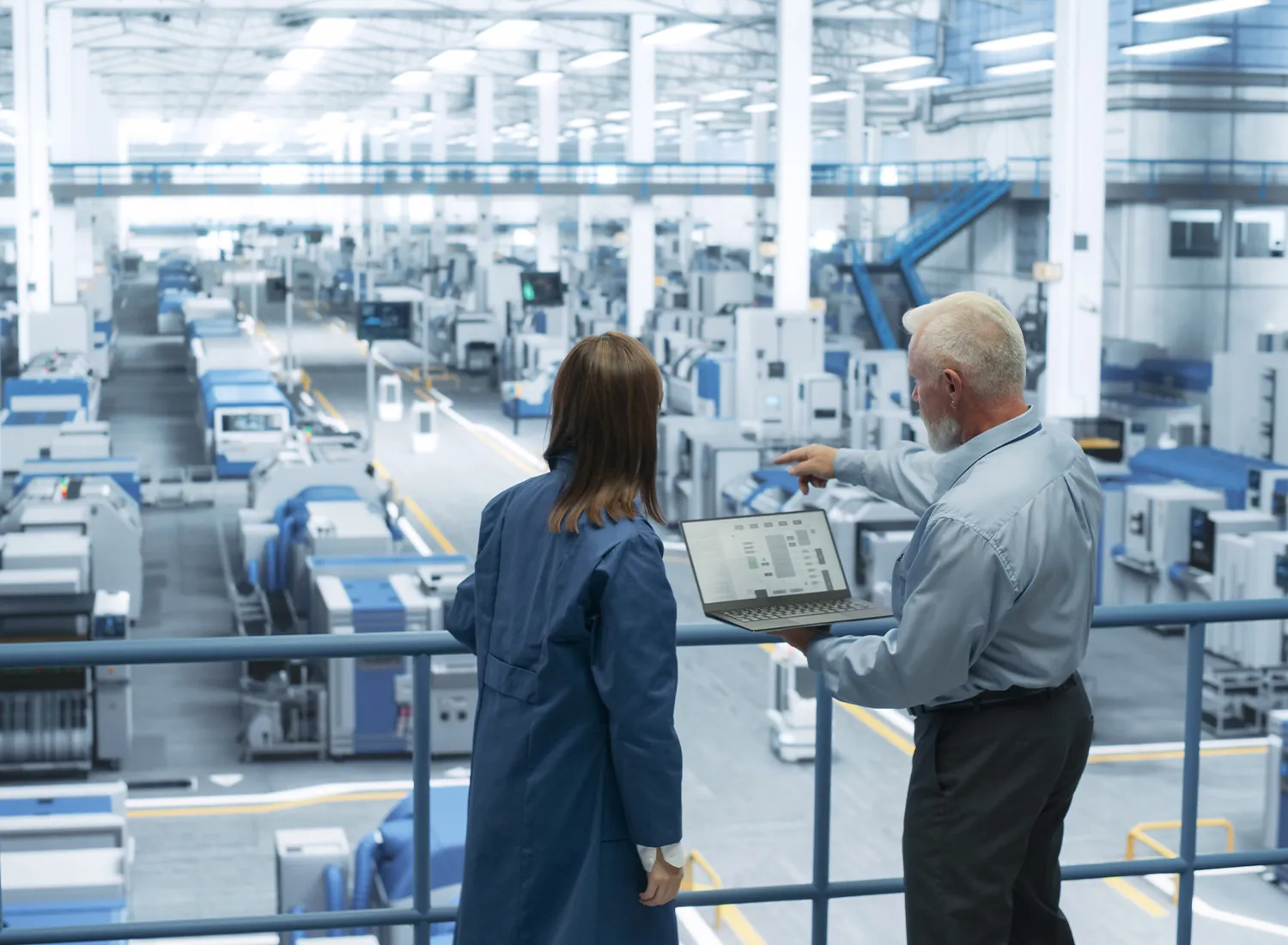
Coordination of production
In addition to selecting the appropriate production technology, we have access to a wide range of machinery with a variety of production options. On request, we can coordinate domestic production, European production and targeted overseas production for you. Depending on the demand situation, item requirements and customer requirements, we communicate transparently here and offer our customers various options in the supply chain.
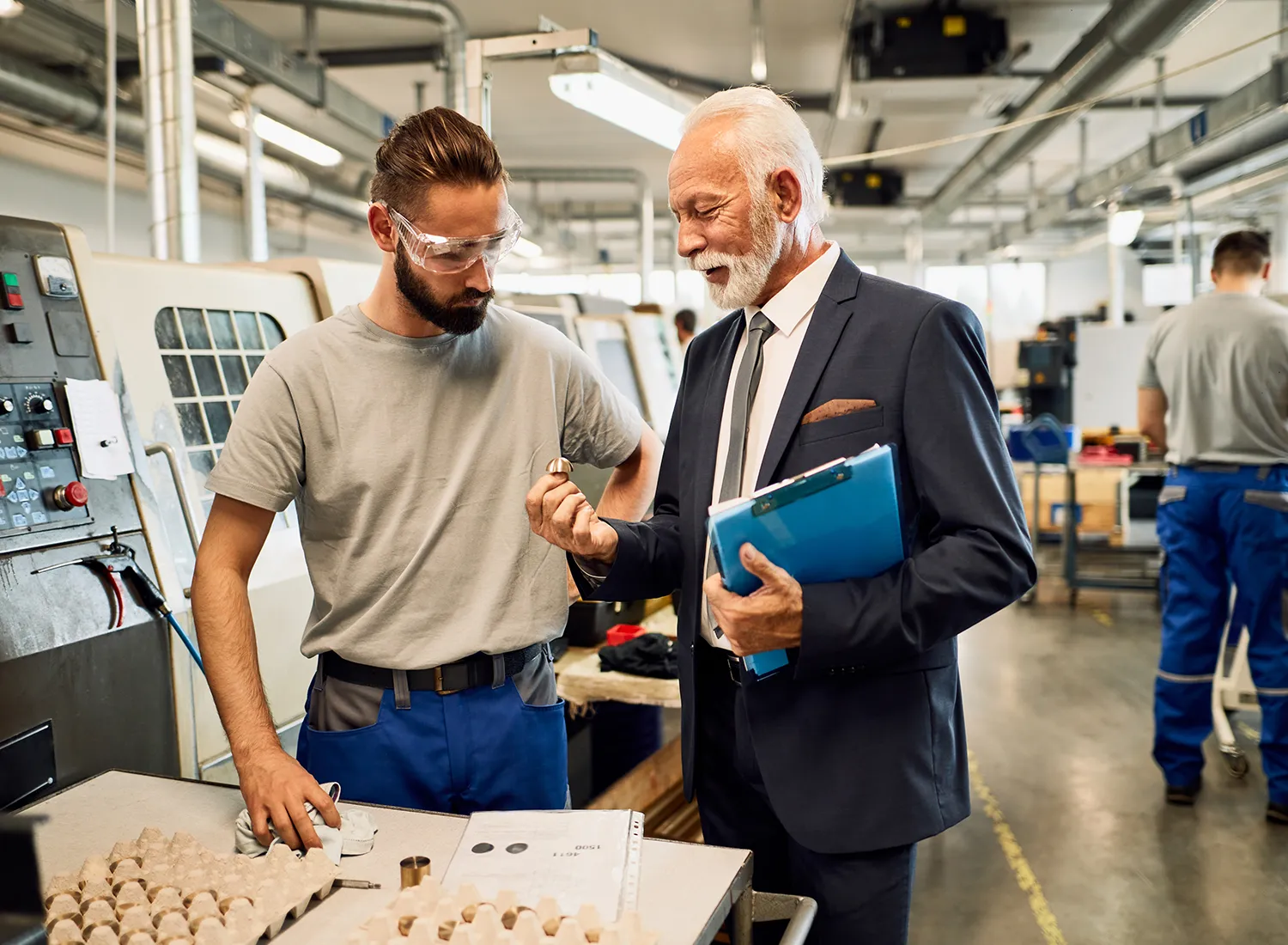
Individually or in combination
The selection of manufacturing processes can be used individually, but can also be used in combination. For example, we can also weld cold formed parts followed by turning or, for example, turned parts with stamped parts in accordance with customer requirements. The necessary coordination of the individual techniques is carried out in-house, so that we can finally deliver a complete solution to our customers.
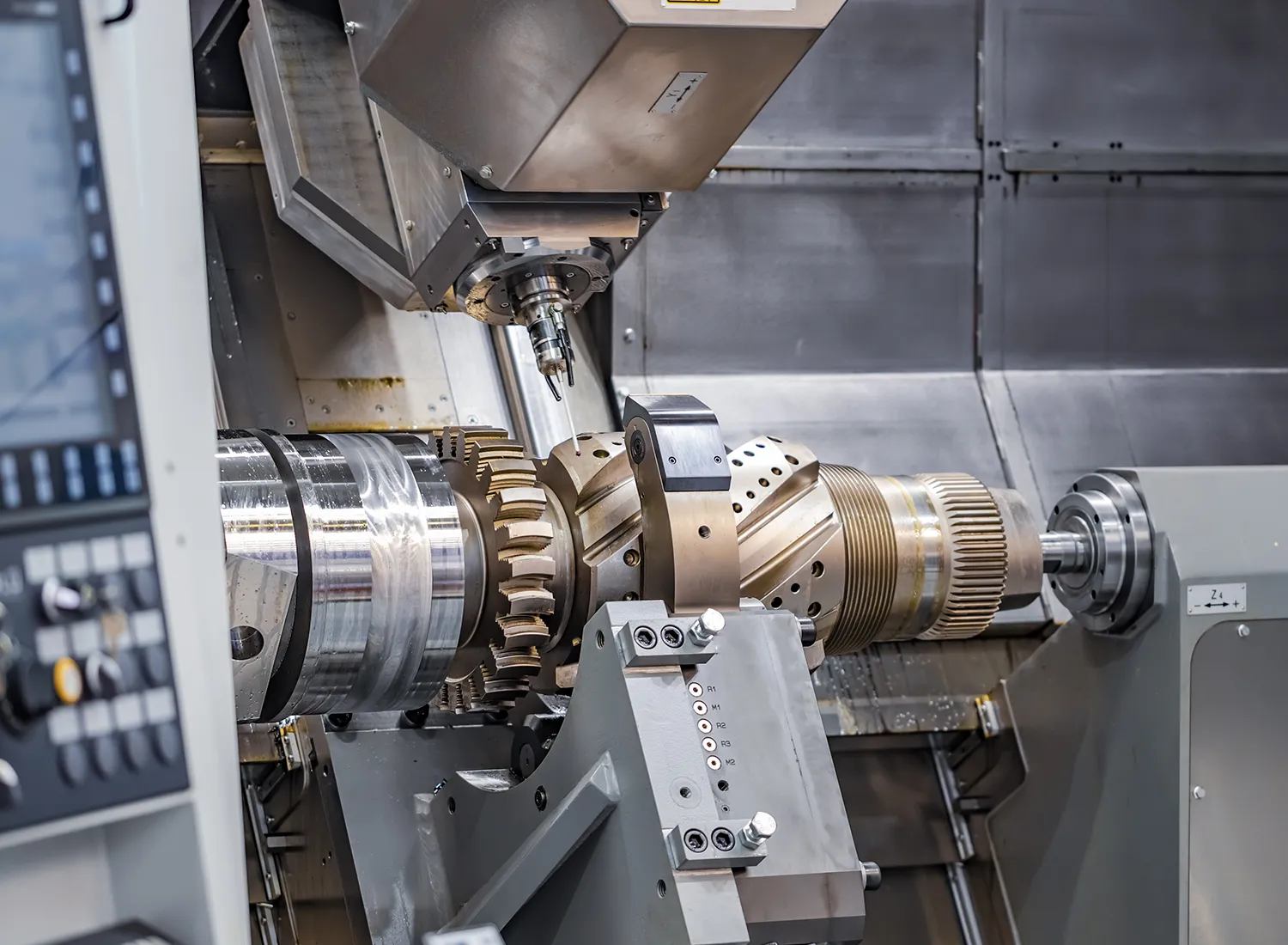
Bent parts
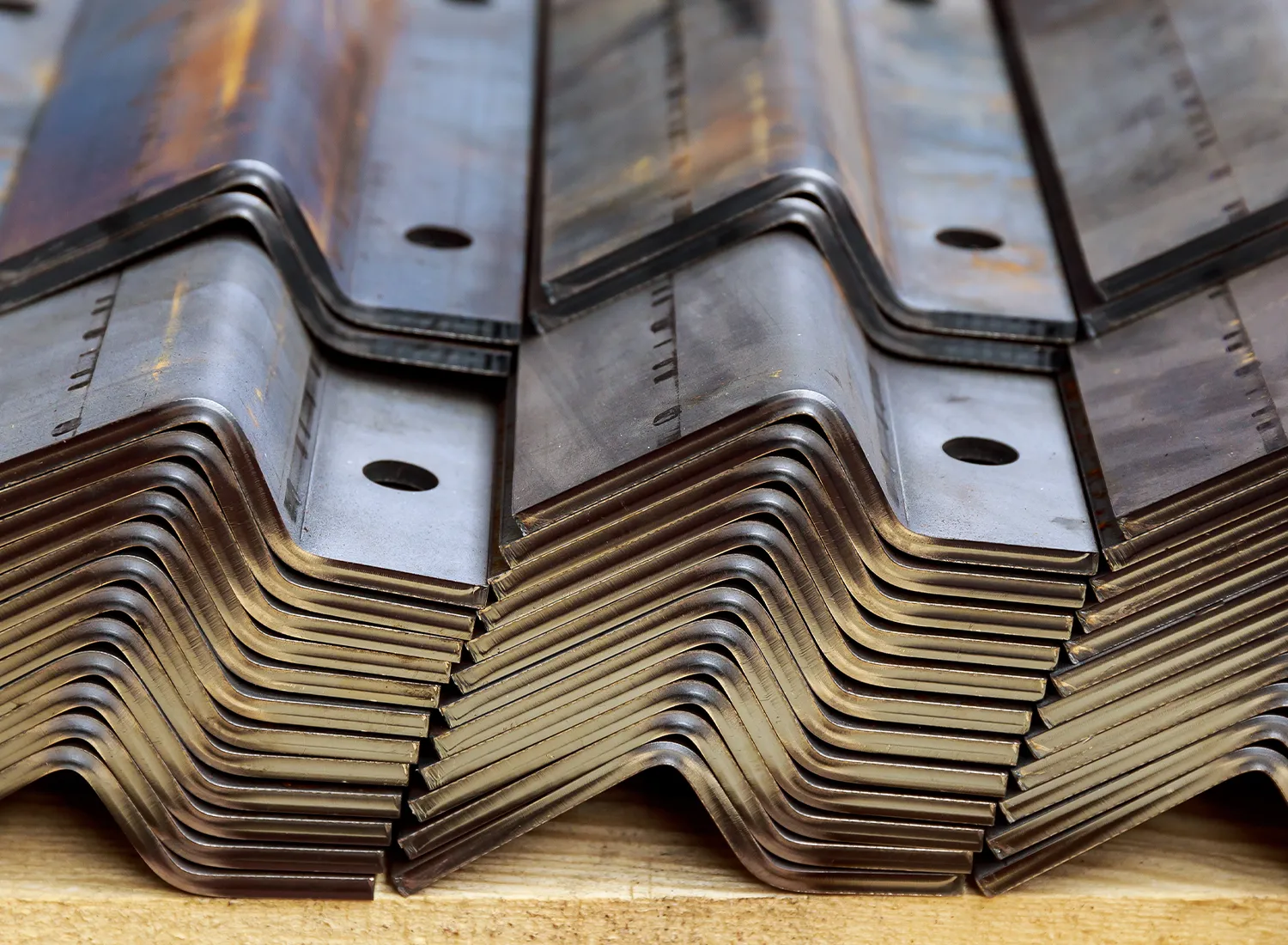
Here, fully automated manufacturing can be coordinated using wire bending and rolling machines as well as combined wire bending and milling systems in order to produce bent wire articles with rolled threads or wire bending articles with milled threads. CNC bending machines and U-bracket machines can be used to produce sophisticated 3D bending articles as well as U-bars, rectangular brackets, roof brackets, double-ended threads or welding ends.
cold formed parts
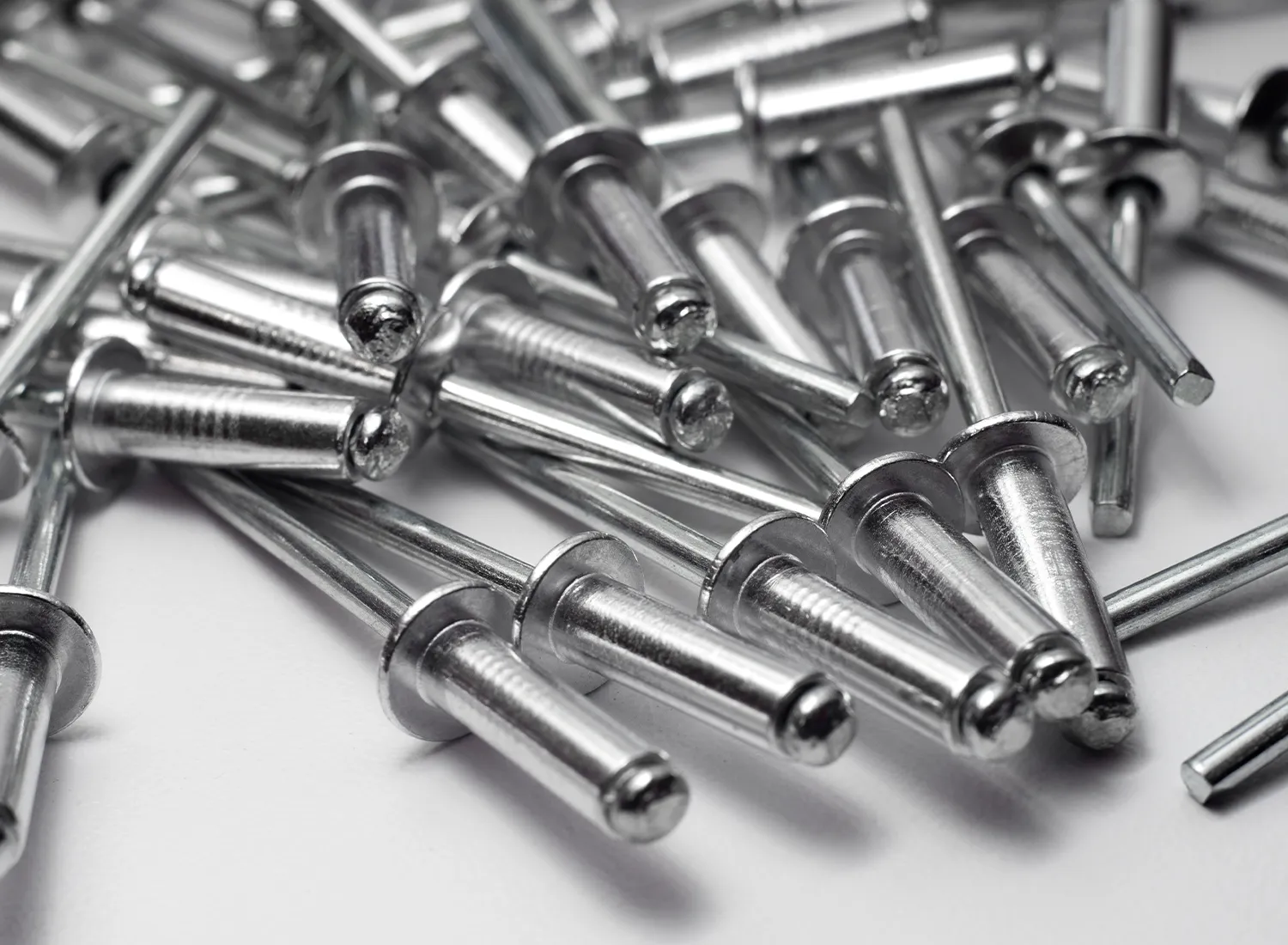
Cold extruded parts are particularly suitable for the production of mass-produced articles (100,000 pieces upwards) such as sleeves, axles, bolts, rivets and tiered shaped parts while saving material. Solid, semi-hollow or hollow parts, complex shaped parts and individual special projects: parts with lug, step holes; with internal/external threads and many other variants are possible. Basically, cold extrusion technology is characterized by the following advantages in the production of precision parts:
- A high level of material utilization
- Manufacturing close to final geometries with reduced rework
- A continuous course of fiber in the component
- High speed in manufacturing large quantities
- High dimensional stability and surface quality
As a result, cold extrusion is particularly effective in the series production of large batch sizes and, due to the resulting economies of scale, offers a generally economical alternative to turning. The dimensions here usually range from 5 to 90 mm in diameter and lengths of up to 240 mm.
Stamped parts
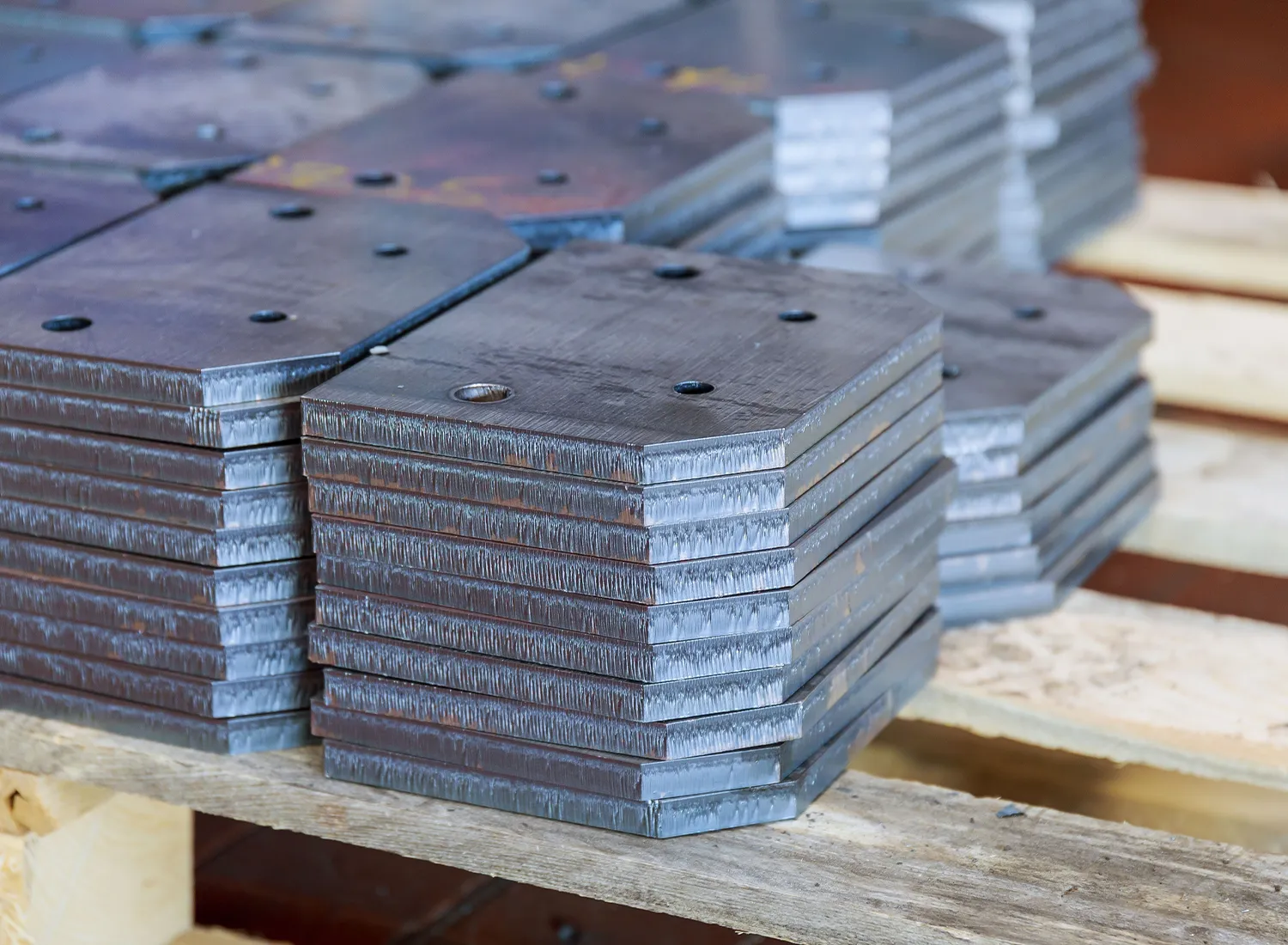
Stamped parts are manufactured from metal sheets, most of our experience in this area lies in the thickness range of 0.5 to 12 mm. Workpieces can be safely punched out of all common sheet metal materials, such as steel, aluminum or stainless steel. First, punched parts that meet the requirements must be designed in accordance with the product requirements and then the corresponding shapes must be manufactured. This usually results in tool costs that are transferred to the individual customer project, which is why special stamped parts in particular usually only make economic sense in larger quantities. Especially with series parts, the tool costs are then amortized quite quickly and the effectively low unit price is usually the decisive factor in practice.
In addition to material preparation, in which the appropriate materials are selected, preliminary work such as cutting, straightening and cleaning is carried out in order to
Stamping process of the traditional punching process: The prepared material is placed in the mold and shaped into the desired shape using a punching machine.
Depending on customer requirements, post-processing work such as deburring, trimming, cleaning and surface treatment is then coordinated accordingly.
laser parts
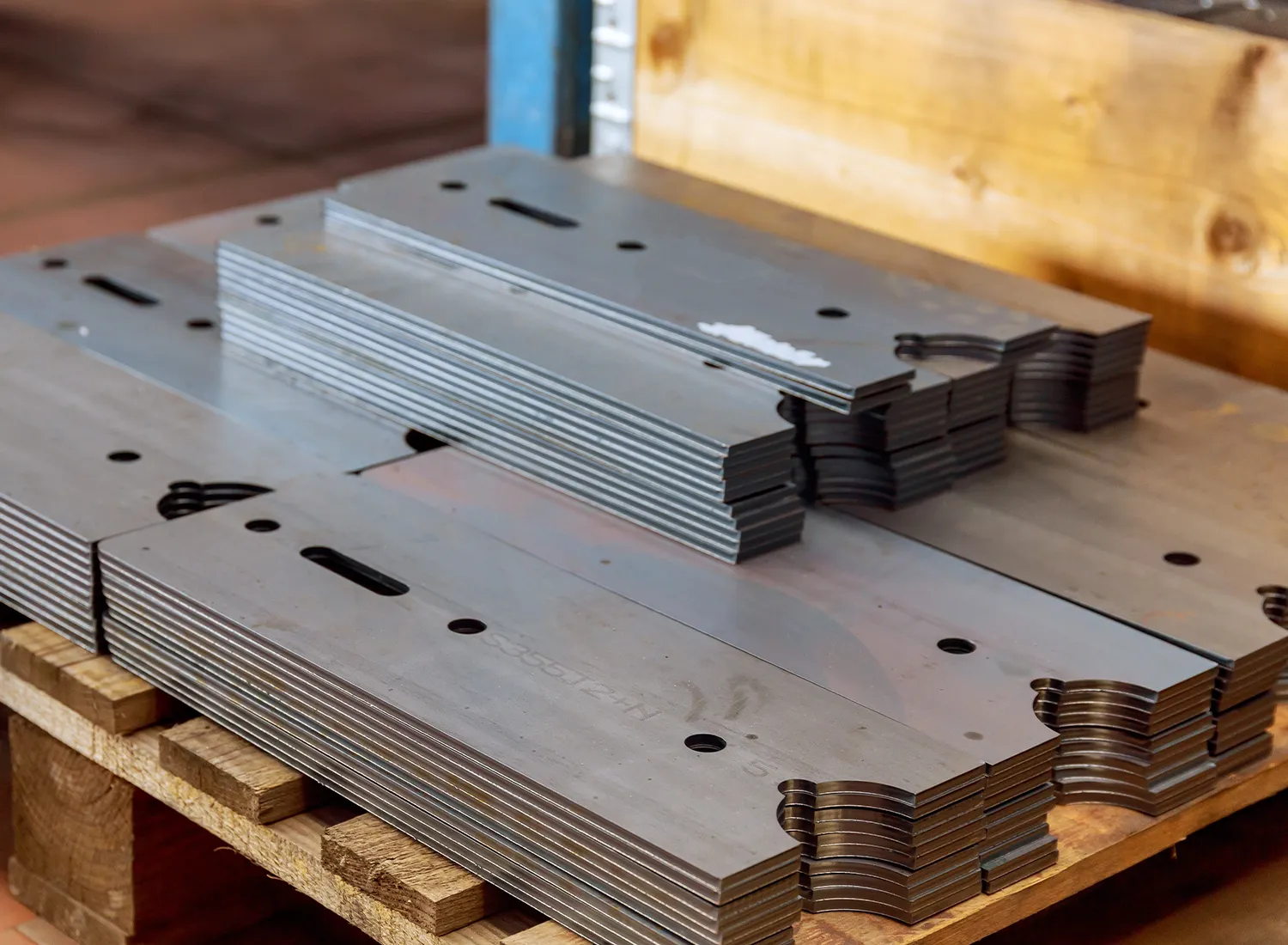
Laser cutting is one of the thermal cutting processes.
Here, too, there are now various modern laser options. Laser work is particularly suitable for smaller quantities that do not yet make sense using a punching process. Threadiness and very high accuracy are clear advantages here. But even with complex shaped parts that can be manufactured via laser — there are modern manufacturing options such as 3D laser cutting. 3D laser cutting enables individual contours and cutouts, as the cutting head is also movable in 5 axes.
3D laser cutting has successfully established itself in metal processing. 3D laser cutting has often been able to replace machining, especially for large workpieces. With appropriate devices, it is possible to produce any inner and outer contours, penetrations, holes and welding chamfers all around the workpiece.
Hot formed parts
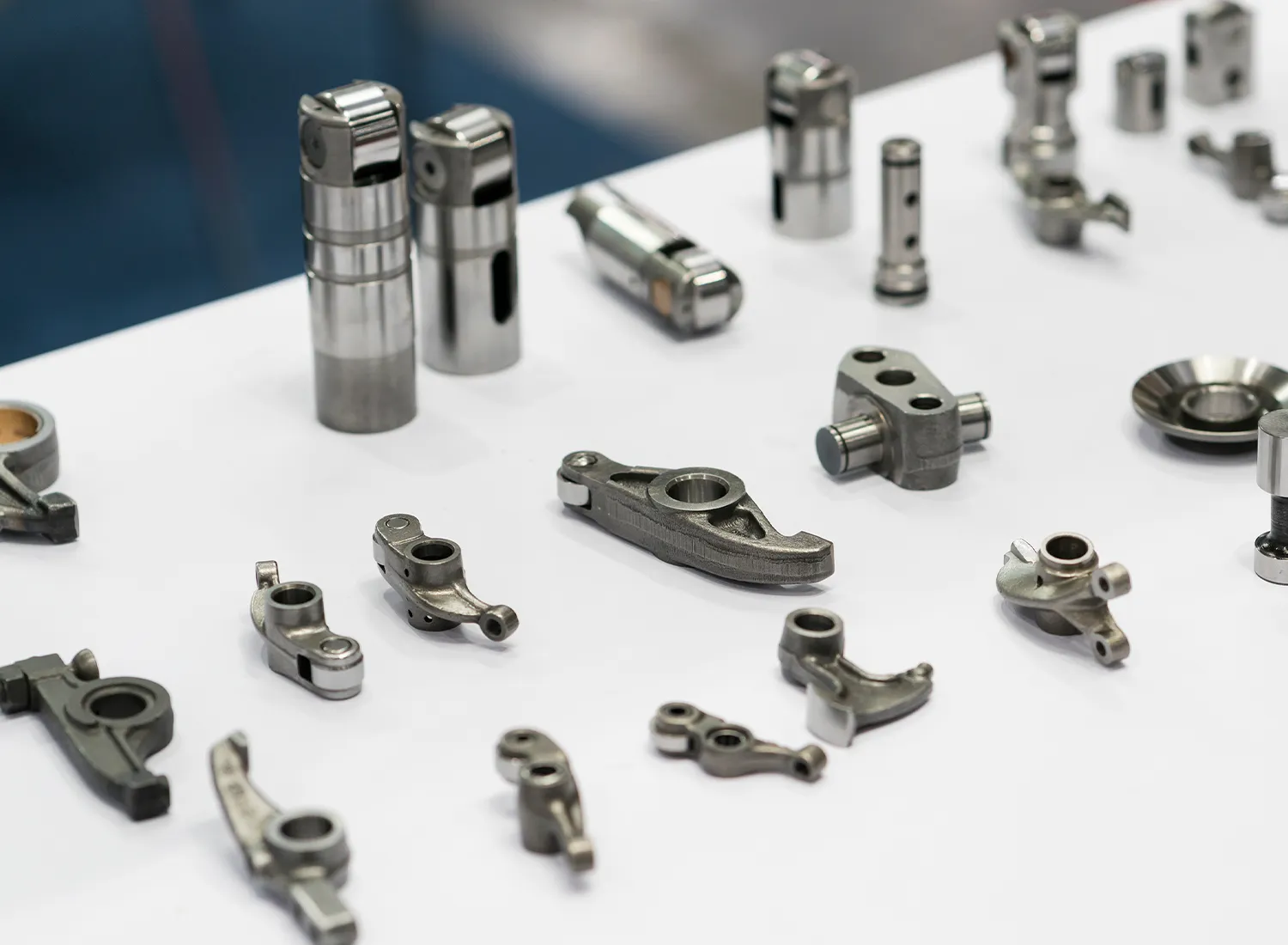
Hot forming refers to all those forming steps that take place above the recrystallization temperature of a metal. The solidification that takes place during forming is accompanied by additional recovery and softening processes. As a result, very high degrees of deformation can be achieved. The material structure and the associated high achievable strength are clear advantages.
It is not absolutely necessary for the material to be heated, as in many metals, recrystallization takes place even at room temperature. Hot forming processes include forging, hot rolling, extrusion and flow drilling. Production is carried out on modern hot forming equipment, which can be supplemented with subsequent turning or milling finishing. Thermoformed parts are particularly recommended for prototypes or small, medium-sized series. The dimensional ranges often only start in a large diameter range (over 36 mm); the articles usually show a “rough” surface structure — the tolerances here are often correspondingly large.
To give an overview of some of the special parts we have manufactured, across all manufacturing processes listed above, we provide a brief overview in the form of article names from our production range:
- Screws in various (special) designs
- stud
- Nuts
- tranches
- metal sheets
- studs
- head bolt
- fret bolts
- expansion screws
- Locking screws
- tubes
- rods
- pins
Benefit from our extensive delivery options for standardized connection parts as well as special parts according to drawings, which are tailored to your needs. Our team of experts will be happy to advise you and find the optimal solution for your needs. Contact us now to find out more and get a personalized quote.